Customer’s Needs
The project of the Datacenter of the University of Strasbourg – Institut de science et d’ingénierie supramoléculaires (ISIS) has one simple objective – to organize the hosting of physical servers while ensuring minimal downtime and the environmental impact. Eco-responsibility was a key conern, with the ambition to make the Datacenter one of the most energy efficient in France, aiming for a PUE (Power Usage Effectiveness) of 1.25. To achieve these goals, above-standard rack cabinets, rack compatibility, efficient cooling systems, and suitable thermal corridors were required, spread across 5 computer rooms and 494 m².
Products and Services Provided by Graziadio
Graziadio supplied compact 2500-3200 and 4000 A K Series lines with aluminium conductors and 250 to 2000 A GDA lines with aluminium conductors to power the cabins and server racks of the Institute’s new data center.
Global Offering
Graziadio’s goal was to exceed expectations in terms of the demanding specification (including reinforced mechanical strength of the busbar), delivery times and flexibility in production schedules and logistics management to enable a rapid start-up of the plant.
Advantages of Busbars in a Data Center
Busways in a data center offer a number of benefits, including greater flexibility in power supply, allowing for easy redistribution of power circuits as power needs change. This system reduces the need for permanent electrical wiring, making it easier to upgrade and maintain. In addition, busbars improve energy efficiency, reducing energy losses and optimizing current flow. Their installation is faster and less invasive than traditional wiring systems, while also offering greater safety by reducing the risk of overload and short circuit. In summary, busbars help create a more scalable, efficient, and secure data center environment.
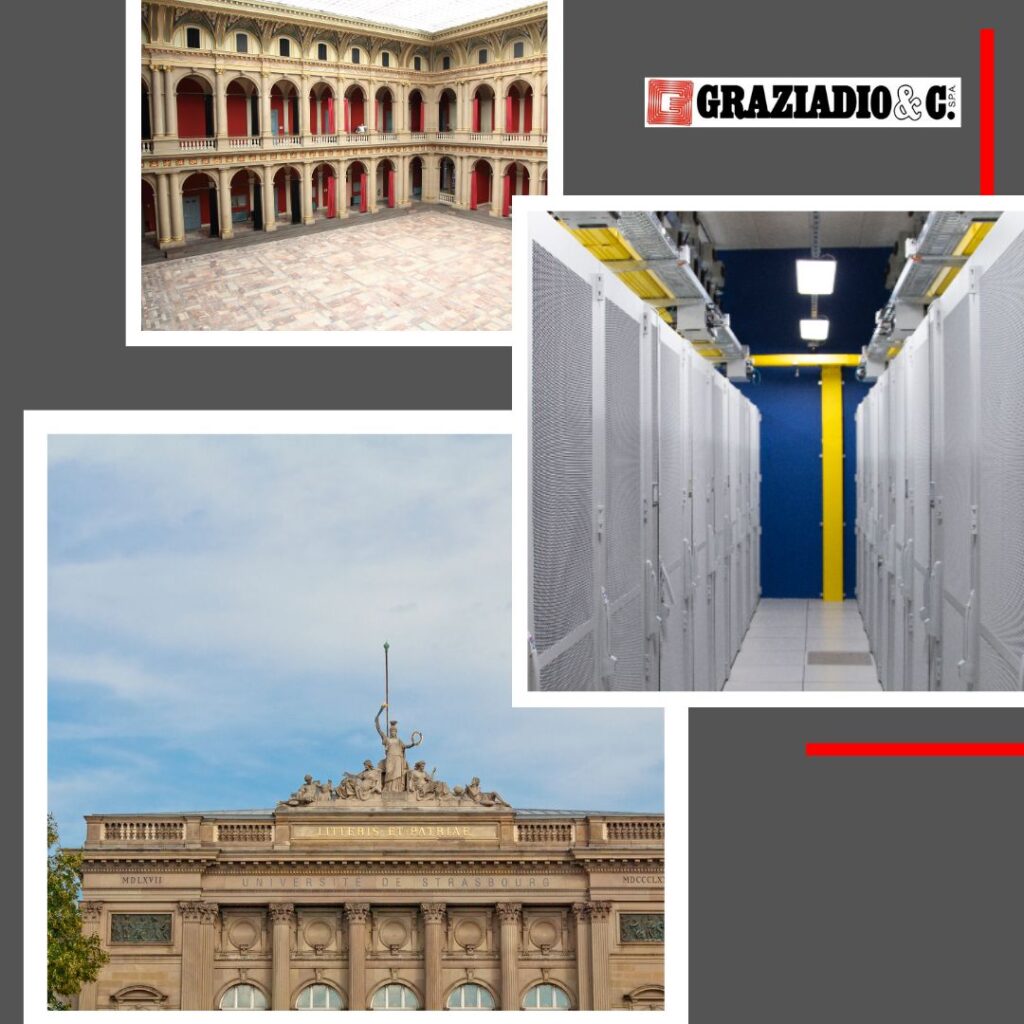